VVER-1200
The up-to-date model of a water-cooled power reactor is developed on the basis of VVER-1000. It is supplied to nuclear power plants in China, Bangladesh, Belarus and other countries. For the first time, VVER-1200 uses unique engineering solutions in the field of safety, which makes it possible to classify the reactor plant as a generation III+ plant.
10 reactors
shipped
12 reactors
planned to be shipped by 2031
Advantages over VVER-1000:
01
2 times longer service life
02
20% higher electrical output
03
Additional security systems
Specifications
3 200 MW
Thermal power
1 200 MW
Electric power
28 800 MW*hour
The amount of energy generated per day with an 18-month fuel cycle
72 hours
Time to ensure autonomy of the plant operation in case of a beyond design basis accident
70 MW*day/kg
Maximum fuel burnup
163
Number of fuel assemblies
Economic characteristics
100 years
Life cycle
90 %
Installed capacity utilization factor
18 months
Duration of work without refueling
35.9 %
Efficiency (COP)
4 years
Overhaul period
Production process
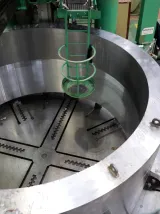
01
02
03
04
05
Production of metallurgical blanks
Bottom stamping
Welding, overlay welding and heat treatment
Machining
Tests
Metallurgical blanks for the reactor vessel are supplied from the AEM-Special Steels metallurgical complex. Large-sized blanks undergo incoming inspection, machining of surfaces and weld grooves on lathes. After the control operations, the blanks enter the following technological stages: assembly and welding.
A flat blank made of pearlitic steel is heated in a furnace at 1000 °C and then placed under a press with a maximum force of 15 000 tf, which forms the bottom of the blank. The double-acting hydraulic sheet punching press is unique and the only equipment in Russia that can stamp bottoms from blanks up to 380 mm thick.
Assembly and joining of two half-vessels and making of the closing weld are one of the key stages of the reactor vessel manufacturing cycle. Welding and overlay welding are carried out automatically using special equipment. Heat treatment of blanks is carried out in gas-flame chamber furnaces to obtain the highest performance characteristics of products.
The machining process includes the manufacture of threaded holes for the studs of the reactor main joint, as well as general work on the finishing of surfaces, welds, nozzles, drilling holes in the internals
During the entire reactor manufacturing process, most of the time is devoted to control tests. Radiographic test equipment is used to detect defects in thick-walled products. The control of welded joints is ensured by means of liquid penetrant and ultrasonic test procedures. In a specially equipped underground stand - a caisson - hydraulic tests are carried out. A pressure of 25.7 MPa (262 atm) is injected into the vessel, in ten minutes the pressure should not fall below 24.5 MPa (250 atm).
In total, hundreds operations are carried out after docking of the reactor half-vessels. Particular attention is paid to nondestructive testing methods.
In total, hundreds operations are carried out after docking of the reactor half-vessels. Particular attention is paid to nondestructive testing methods.
Supply references
Bangladesh
| Rooppur Nuclear Power Plant | Unit No. 1,2 | VVER-1200
|
Belarus
| Belarusian NPP | Units No 1, 2 | VVER-1200
|
China
| Xudapu Nuclear Power Plant | Unit No 3 | VVER-1200
|
China
| Tianwan Nuclear Power Plant | Unit No 7 | VVER-1200
|
Russia
| NPP Leningradskaya-2 | Units No 1, 2 | VVER-1200
|
Russia
| Novovoronezh NPP | Units No 6,7 | VVER-1200
|
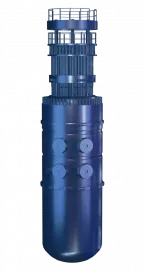