Manufacturing of PCFS hydroaccumulators
1
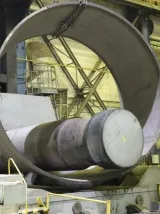
Shells used for assembling the bodies of hydroaccumulators are manufactured in the assembly and welding production area of Petrozavodskmash. Each PCFS accumulator consists of three shells and two heads. The shells are made of 60-mm thick stainless steel sheets. For one accumulator, a cylinder of 4.3 m diameter is made of a 2.5 m wide and 13 m long blank on a bending machine. For a set of eight PCFS accumulators, 24 shells are required.
Three PCFS shells are assembled and welded to the head by circumferential welded joints. In the resulting semi-bodies, internals, floorings and ladders made of round bars are installed. One flooring reaches 4 m in diameter and more than 400 kg in weight. Each accumulator accommodates three such structures. At the end, the top head is welded. After hydraulic tests, the accumulators are cleaned and prepared for painting. Painting, preservation and packaging complete the procedure of manufacturing the accumulators.
Embedded components and fasteners are metal annular supports made of steel sheets with a diameter of about 5 meters and weight of 9 and 18 tons each, respectively. The embedded components are concreted into the NPP ceilings; the fasteners are attached to them, and the hydroaccumulatos are installed on the fasteners. To fix eight hydroaccumulators at the NPP, eight embedded components and eight fasteners are required. The total weight of the equipment is 220 tons
Before shipment, the PCFS accumulators undergo several checks such as load tests, hydraulic tests, and visual inspection. The hydraulic tests are used to check the finished structures for strength and tightness. The quality of the welded joints is controlled by dye penetrant test. In addition, outer surfaces of the hydroaccumulators are visually inspected for deformations and leakage.